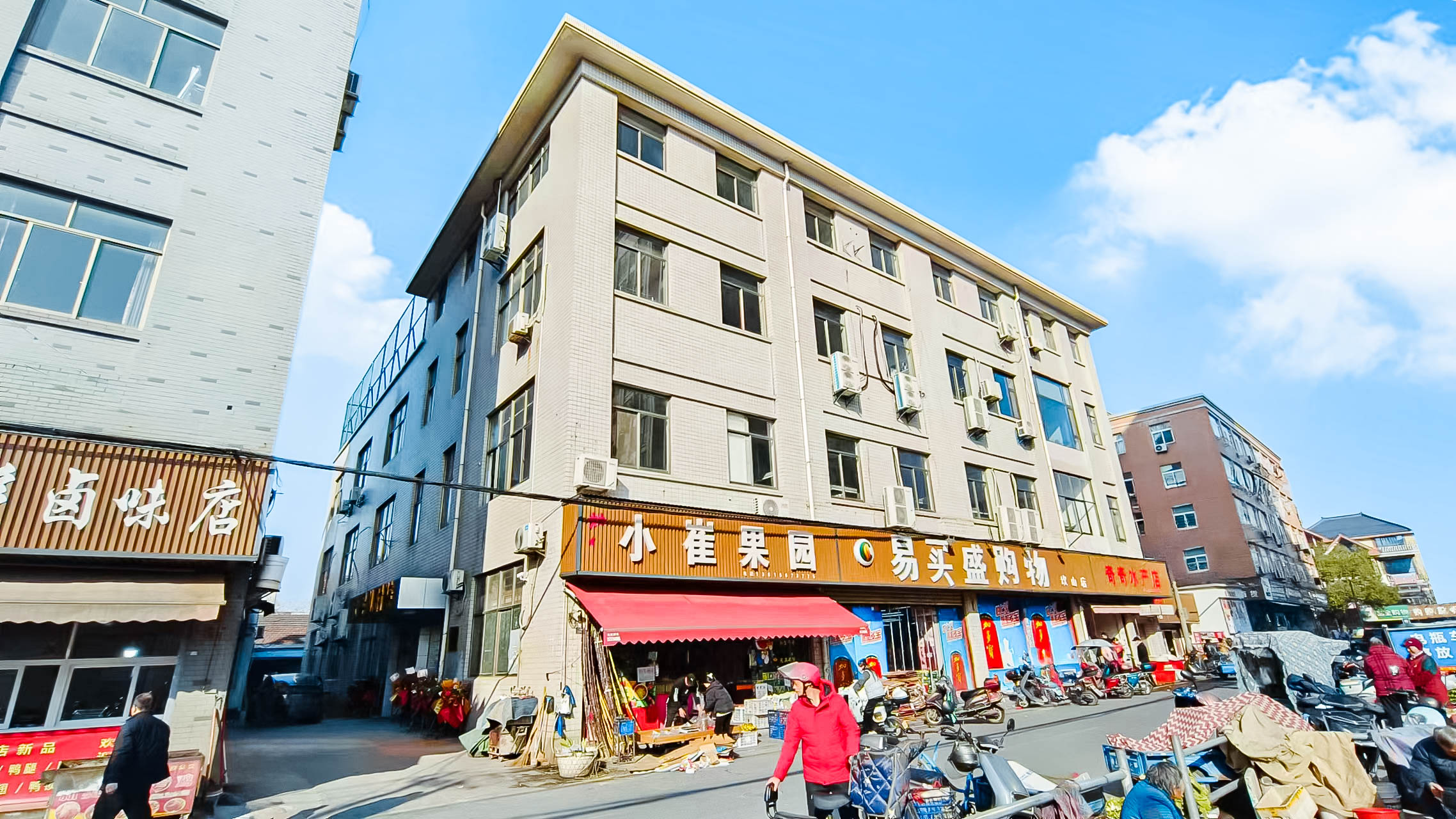
Service
Frequently-Asked Questions
Yes,Hangzhou Ciny Fashion is based in Hangzhou, China and we produce in our factory locations in NO.5, XINBA ROAD, BADA VILLAGE, GALI TOWN, XIAO SHAN DISTRICT, HANGZHOU, CHINA 311219
Our factory specialises in ladies and kids garments
1/ With the small quantities produced, there will be variances in dye and print colours. We will work towards matching very closely; however, we suggest that customers use a disclaimer/special swing tag to inform the end consumer about the handmade nature of the garments and that therefore irregularities in colour and makeare part of the process. This is particularly important in special dyeing and wash techniques where each garment will be different and unique along the production line.
2/ A 3-5% variation in production quantity is within a normal range of overproduction and/or rejects, and we will advise these qty’s before shipment & ship them without further notice.
3/ A 3% reject rate is industry standard and is considered normal. Our efforts will always be to deliver 100% perfect production runs to the highest of quality, however there will be no refund for any minor faults below 3%.
4/ In case we have pieces that are rejected in our QC, we will offer them to you for a 30% discount (if the problems are minor enough), or, if you don’t want to take them, we will resell or get rid of them without further notice (without the brand label).
5/ Complaints for goods can only be accepted within 14 days after the goods have been received, for either a discount, replacement, or credit. Customers are required to provide a report with the number of defects and supporting imagery. We will have to confirm, after we receive proof, that the fault is from the production. The return shipping cost is borne by the customer.
6/ If the claim of damaged goods has occurred during transit from our factory to the customer’s destination and is not from our production, we are not able to bear the cost of a re-make and we advise the customer to get into contact with their cargo insurance provider. As per our trade terms of EXW or FOB, we transfer responsibility of the production to the customer once the goods leave our factory location for EXW or at the nominated shipment port for FOB. It is the responsibility of the customer to invest in a suitable cargo insurance for the total value of their goods.
7/ We bear the responsibility to re-make or refund all complaints/defects that are due to our fault in sampling or production and will give the best solution possible to the customer to ensure a long-term relationship.
8/ For production orders above the value of $30,000 USD, a 3rd party quality control firm may be hired by the customer if requested, however this will need to be discussed and confirmed prior to the production commencing. The customer will be required to cover all expenses in relation to the 3rd Party QC booking and will need to ensure the booking date/time and availability will work with our manufacturing staff and management.
1/ For sampling, we will full including specification sheets.
2/ For prints, we will need final ai, eps or PSD artwork, either sent to us by email or WeTransfer. If specific colour matching is required, it is the responsibility of the customer to provide pantone TPG/TPX codes or swatches for colour matching. Any print costs incurred eg. preparation of screens, low MOQ or strike off fee’s will be charged for and payable by the customer, unless otherwise included in your bulk production cost. Print Screen fees can vary pending on print technique from $35 USD to $50 USD each color.
3/ For colour, we can match to stock fabrics, pantone TPG/TPX codes or the customer can send us swatches via courier for matching. Please note there is a 2-3% shade tolerance to matching to swatches depending on fabric quality and type. For custom colours, matching to pantone or swatches in a lower MOQ, a dye fee will be incurred per colour and per fabric quality at approximately $40-$80 USD each.
4/ Sizing/Grading is the responsibility of the customer, we can provide a specification with the customers grading rules, which will need confirmation before we grade the patterns, however we do prefer the customer to supply the grade rule to us for a more accurate sizing chart.
5/ The customer is required to pay for all sample shipment fees to and from the factory & we will ship samples, once the payment for those has been received in our bank account. We suggest all customers to use a reliable international shipping courier such as DHL,UPS,FEDEX.
6/ In order to process the customers sample comments we recommend the customer to provide feedback in the sampling report document (or similar). Alternatively, you can engage Ciny Fashion to assist you with the sampling reports to ensure your communication of changes and approvals are accurate and clear.
1.Proto Sampling
Sample Fee: Average proto sample fee is $30-80 USD per style depending on the design complexity, proto sample can be substitute/similar fabric and substitute colour.
Sample Lead time: 7-14 Days depending on fabric and design complexity
Sample Pattern Charge: Covered in the provided sampling fee
2.SMS Sampling (if required)
Sample Fee: SMS sample fee, 2x of the FOB cost per style/per colour
Sample Lead time: 30-45 Days depending on fabric, design complexity and order qty.
3.PP Sampling
Requires a 30% bulk deposit down payment, samples are cut from bulk fabrics and trims (if available within the timeline required to submit PP samples for approval)
Sample Fee: PP Sample fee is 1x of the FOB cost per style/per colour
Sample Lead time: 25-30 Days depending on fabric, design complexity and order qty.
4.Shipment Sample
Are shipped 1 week prior to bulk production being finished for client approval
Sample Fee: Shipment Sample fee is 1x of the FOB cost per style/per colour
1/ All our prices are FOB or EXW, DDP ,DAP prices as listed on your quotations and/or invoices.
2/ Our minimum order QTY’S are as follows and can be variable based on the fabric quality, colour/print MOQ’s and complexity of construction. We can provide a more accurate MOQ once the customers tech-packs are provided.
Ladieswear: 100pcs per style/per colour, depending on design, fabric & trim
Menswear: 100pcs per style/per colour, depending on design, fabric & trim
Kidswear: 200pcs per style/per colour, depending on design, fabric & trim
3/ All prices are based on current fabric prices. Fabric prices can fluctuate and we do not take responsibility for price rises between the day of quotation and placement of order.
4/For sampling we do not pay for any shipping or freight costs (this includes any samples, swatches, artworks that need to be sent) and will use the customers nominated courier account. For production, we will work with the customers appointed cargo, or ship with their courier.
5/ We can ship samples, swatches & artwork to the customers nominated address.
6/ Sample payments are 100% upfront before we commence pattern making & sampling. Please make sure the details on all transfer slipes are correct to avoid any delays in commencing the project.
8/ PP Sampling & Production requires a 30% deposit followed by full payment once the order has been completed. If an order is split in delivery, a 30% credit balance of the order value must remain in our account.
1/ Production lead time is 30-45 days once all bulk fabric and trims have arrived at our factory. Production can only start once all samples, fabrics, trims & size specs have been confirmed and the deposit payment of 30% has been received in our bank account from the customer.
2/ If the production delivery changes, or if fabric/accessories suppliers cannot deliver within the timeframe needed, we will need to re-schedule the production to our next availability in the production line and will contact the customer immediately to ensure a prompt solution.
3/ Production for all orders at 100pcs per style/colour or under are required to be made during our factories low season from March to September. Sampling is welcome all year round, however, you may experience some delays in the busy months of Oct, Nov, Dec, Jan & Feb.
4/ Re-orders are subject to fabric and colour availability. Our MOQ for reorders are 100pcs per colour/per style and can be produced within a 4–6 week lead time if all suppliers can deliver on schedule for the Cut, Make & Trim timeline.
1/ Garments will be sent folded in a cardboard box, each in a single plastic bag. Any special packing requirements will have to be paid and supplied for by the customer.
2/ We will supply basic care-labels. The content of the care label is the responsibility of the customer, we will print according to your instruction or as provided by your final buyers.
3/Main labels/Hangtags will be supplied by the customer. If you do not meet our suppliers MOQ or have speciality requests, Ciny Fashion can also help arrange the sampling and production of trims at a smaller MOQ pending the country of manufacturing.
4/ If we are not supplying labelling or packaging, it is suggested to provide all trims/labelling/packaging prior to PP Sampling submission and commencement of bulk production so we can sew them in when production starts. A delay in supplying labels or trims will delay the customers delivery date.
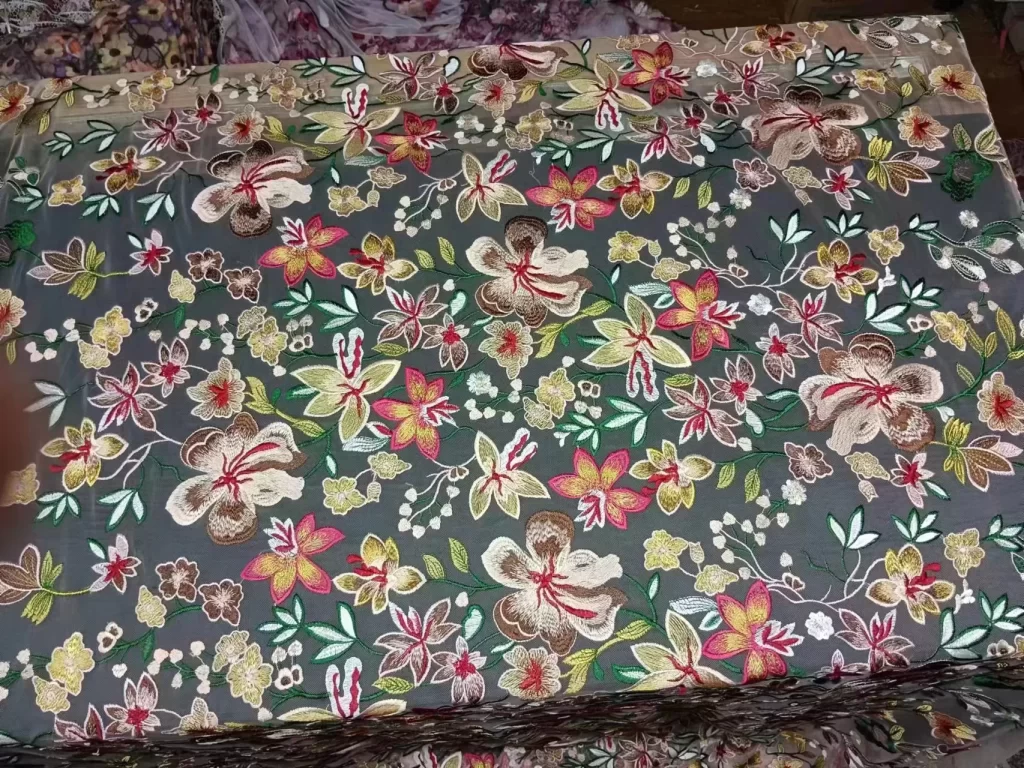
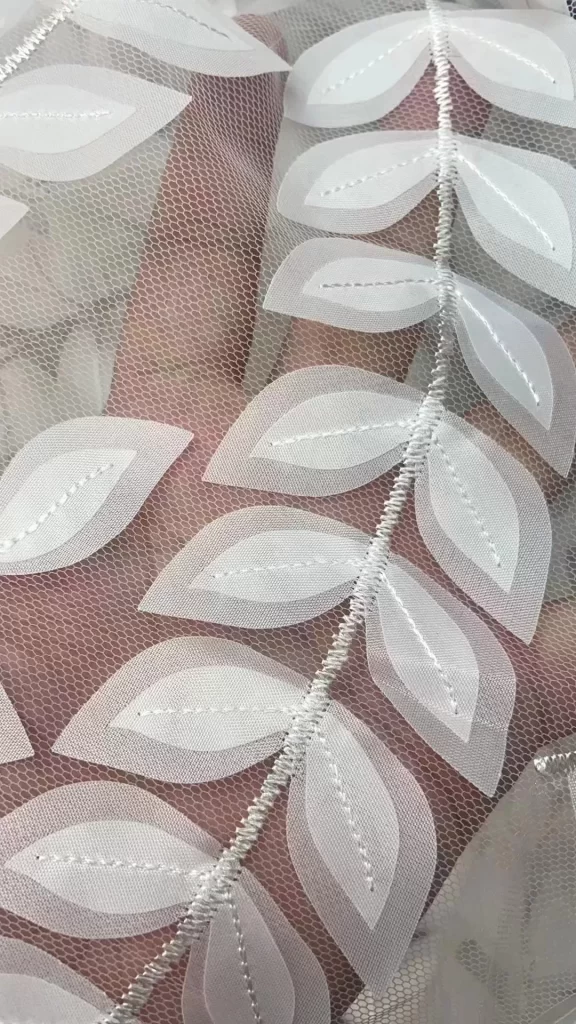
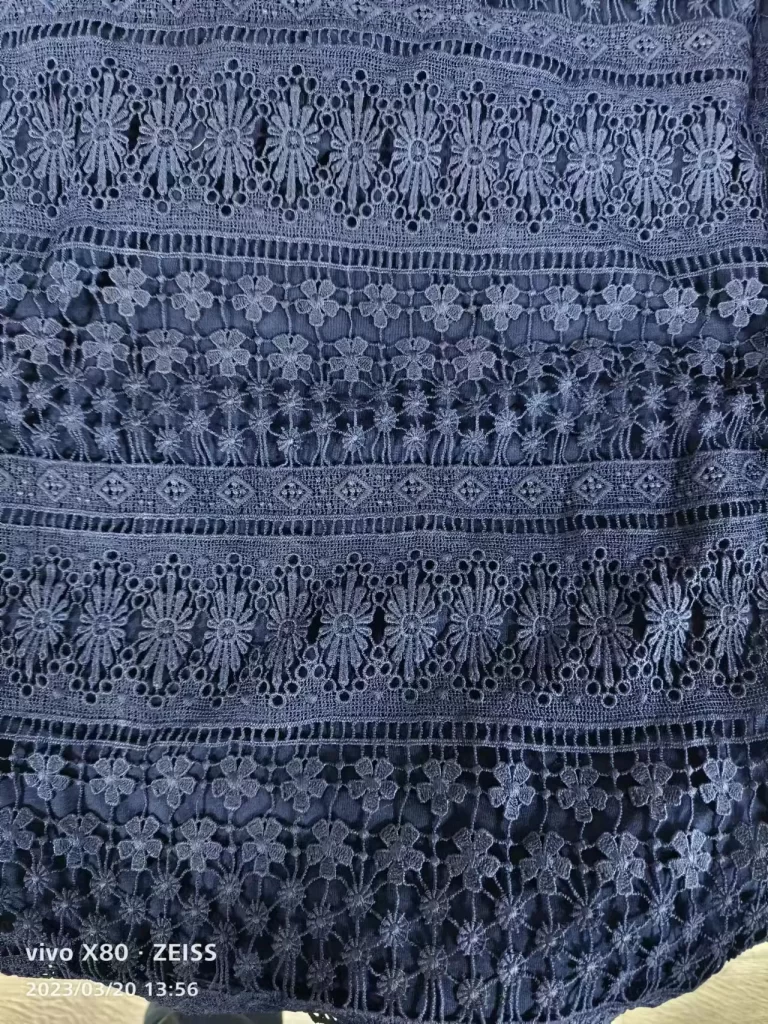
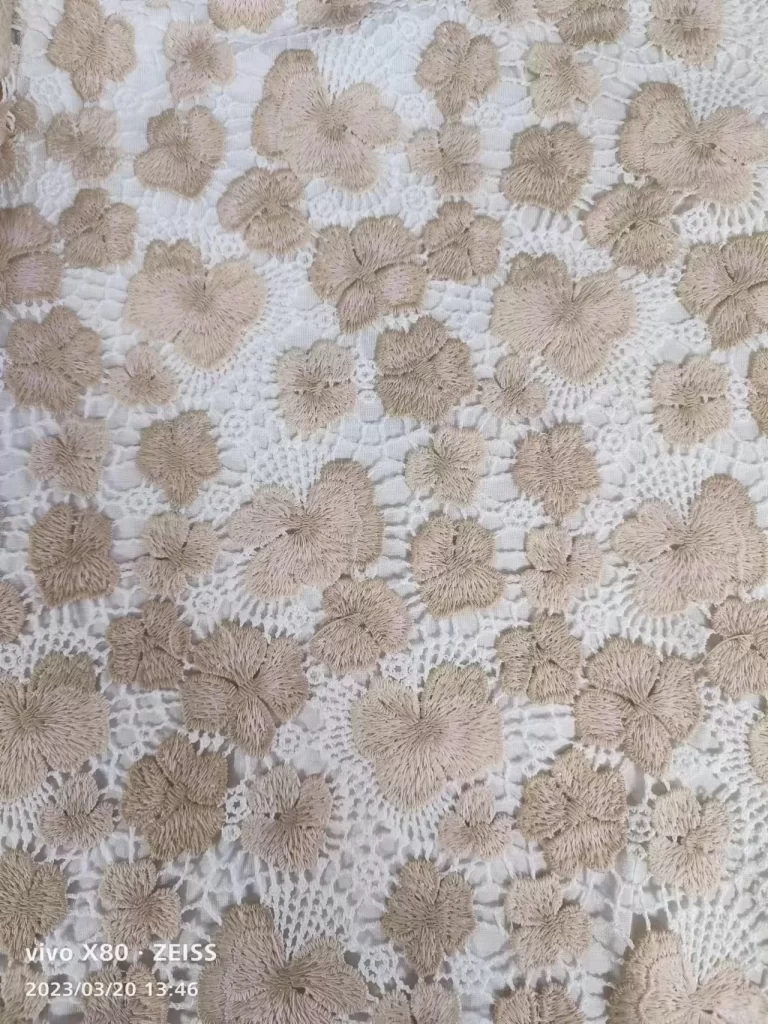
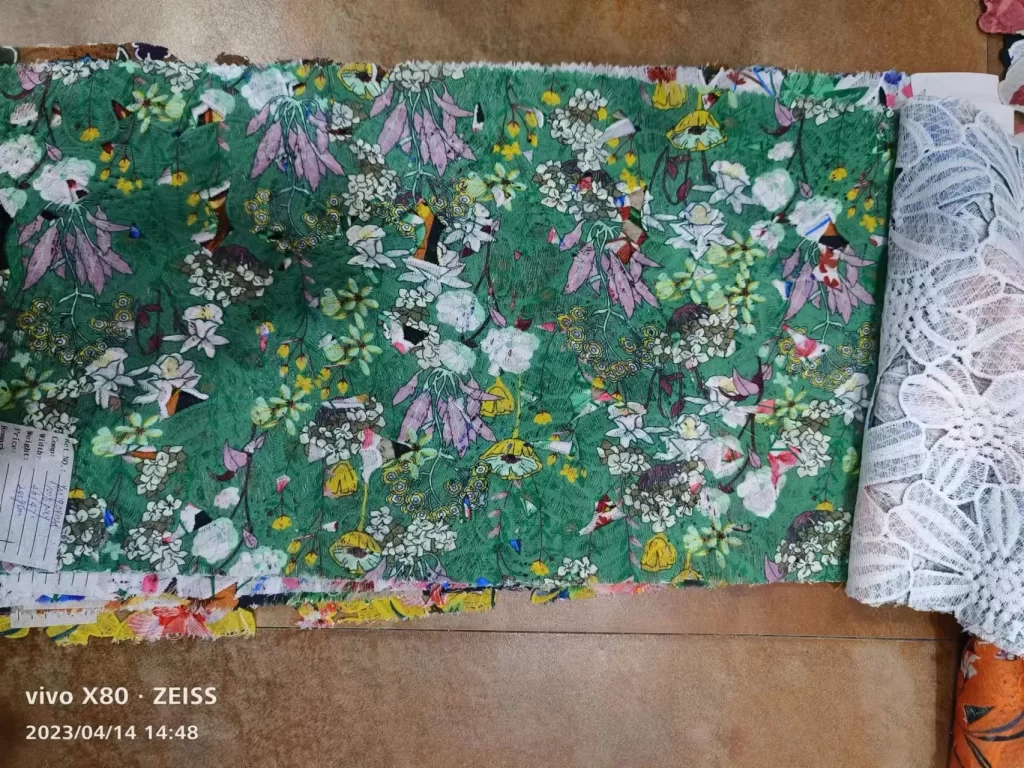
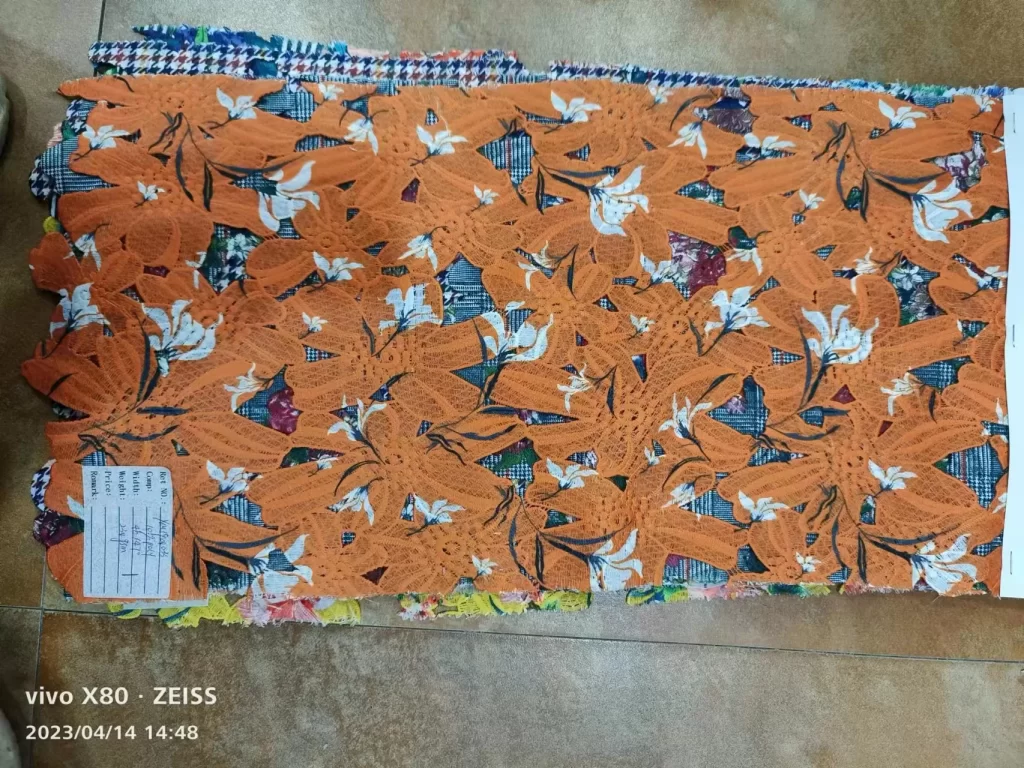
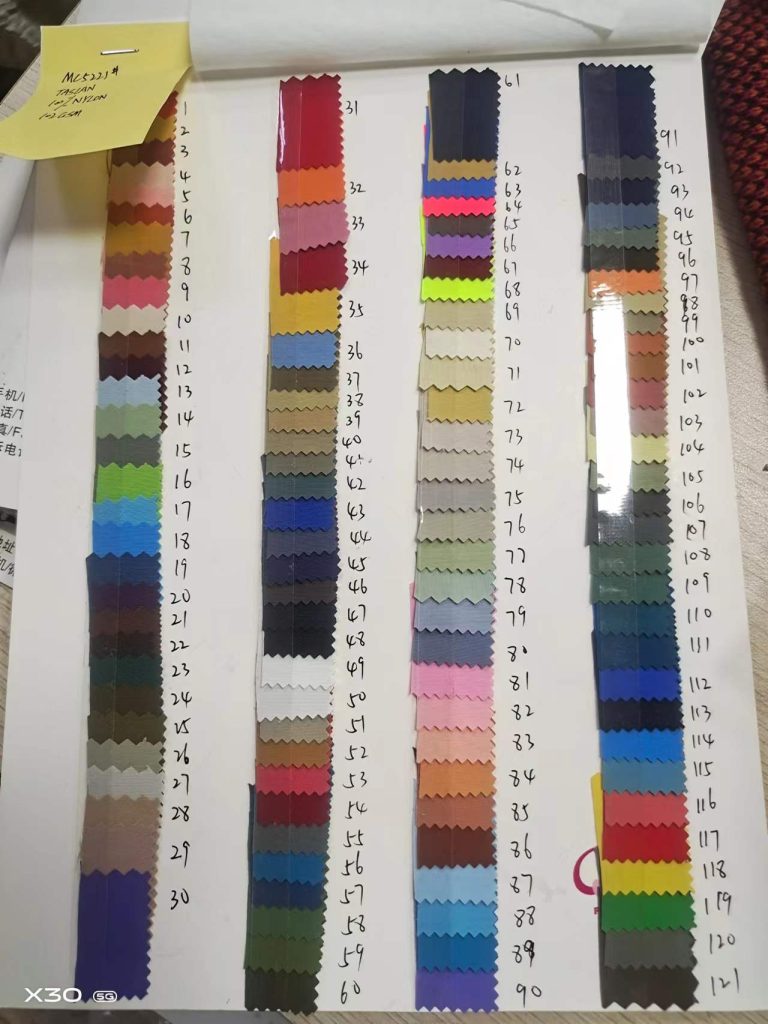
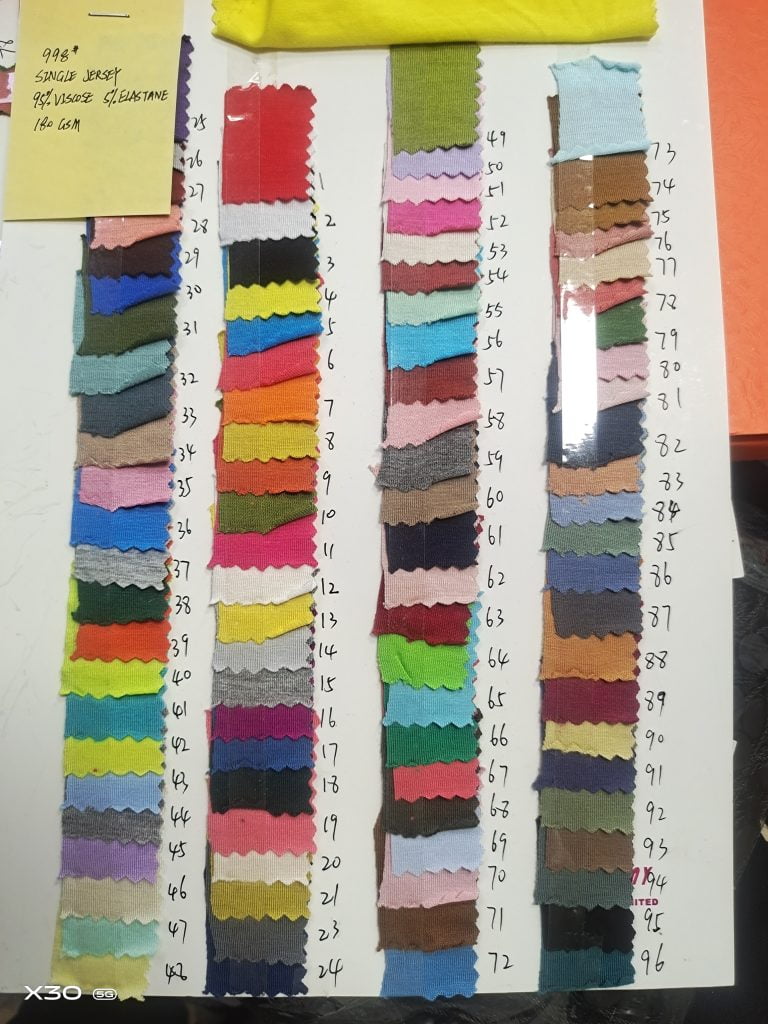
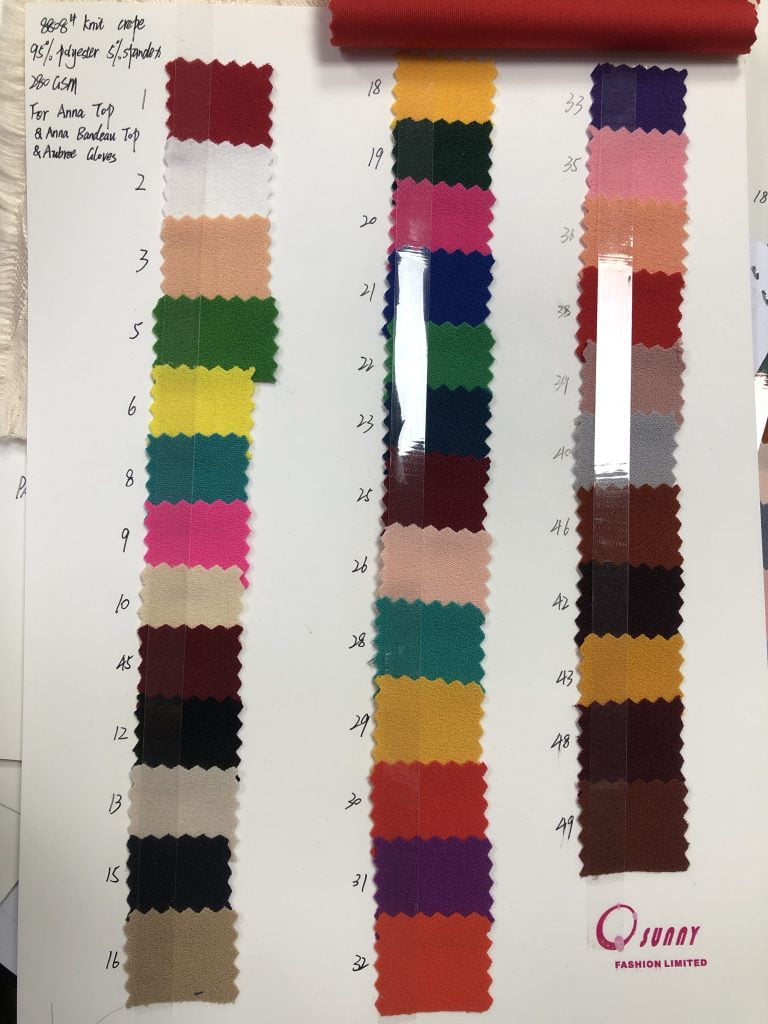
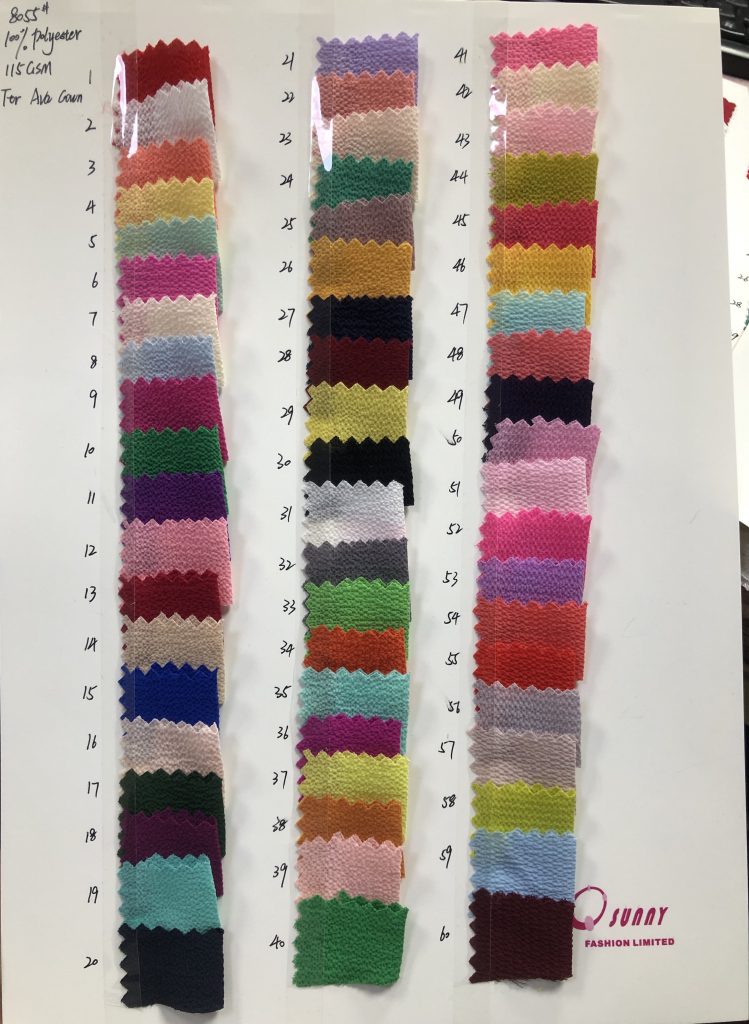
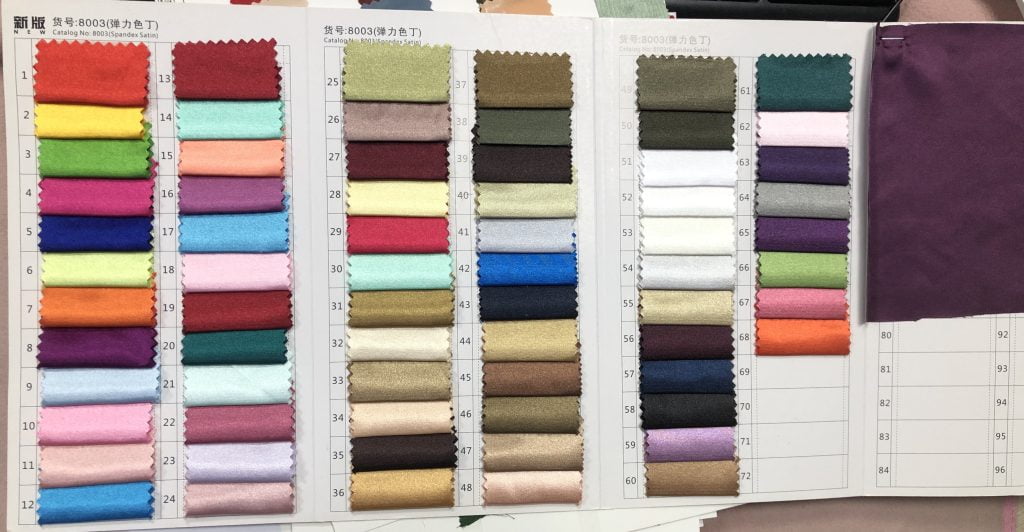
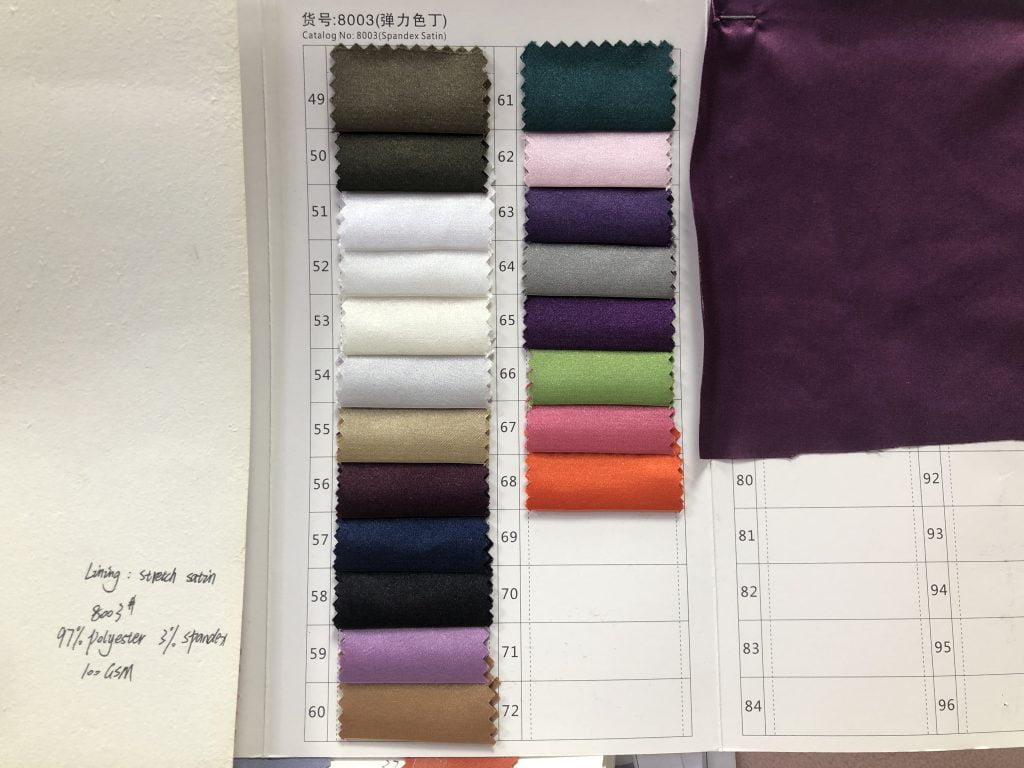
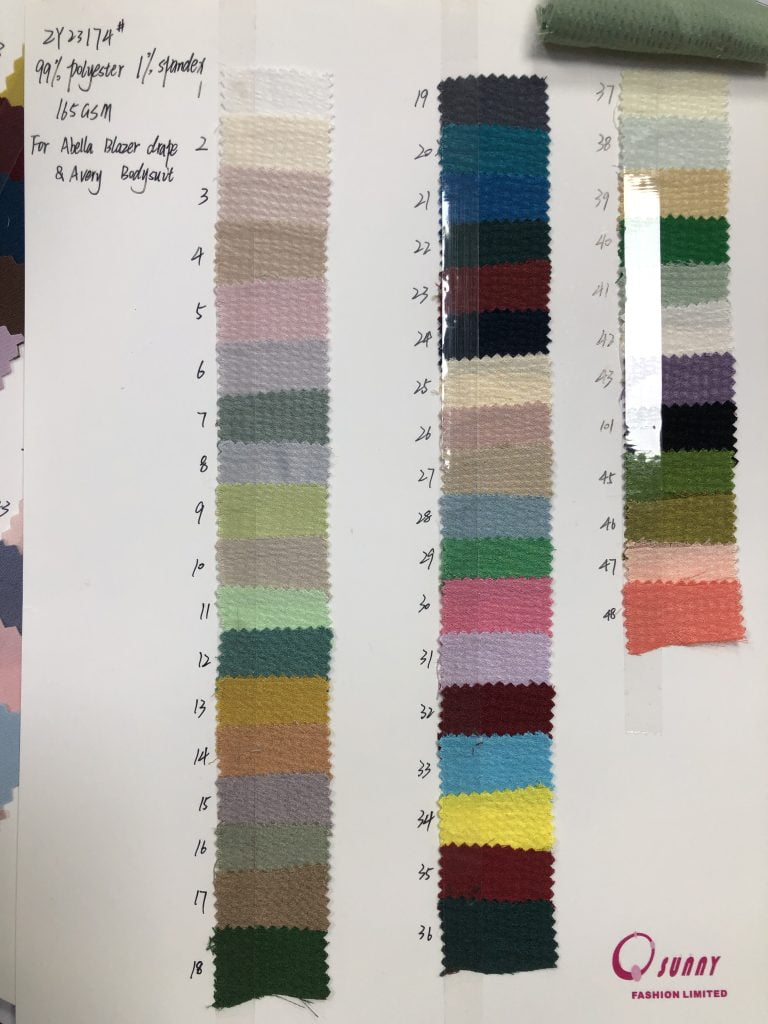
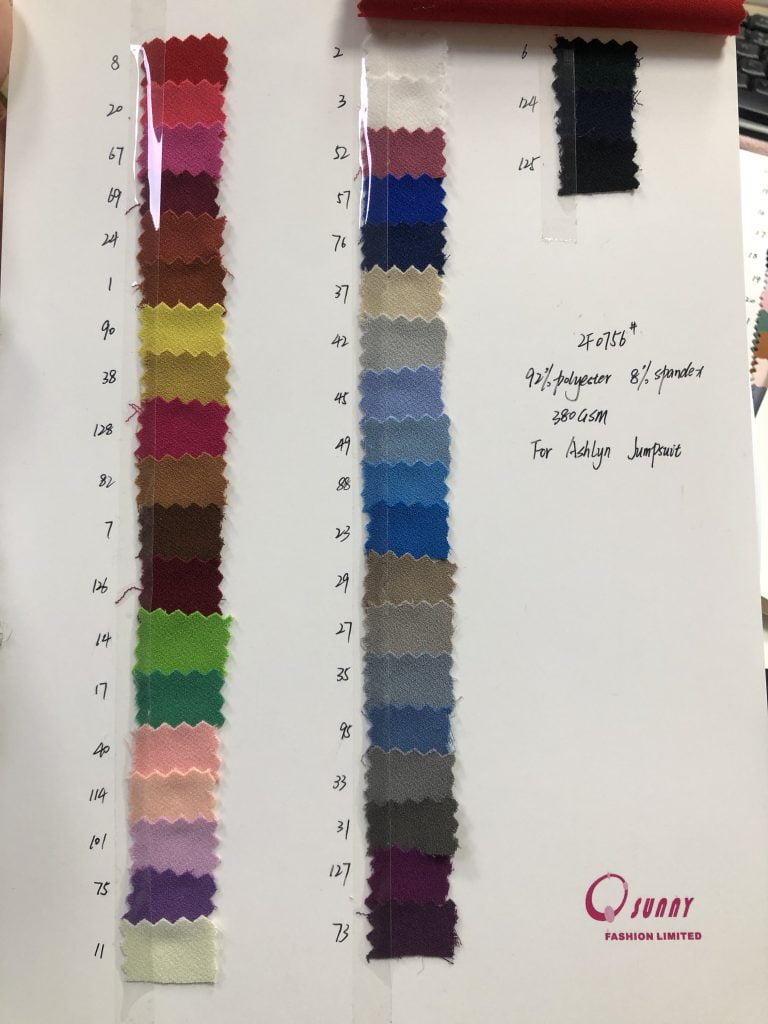
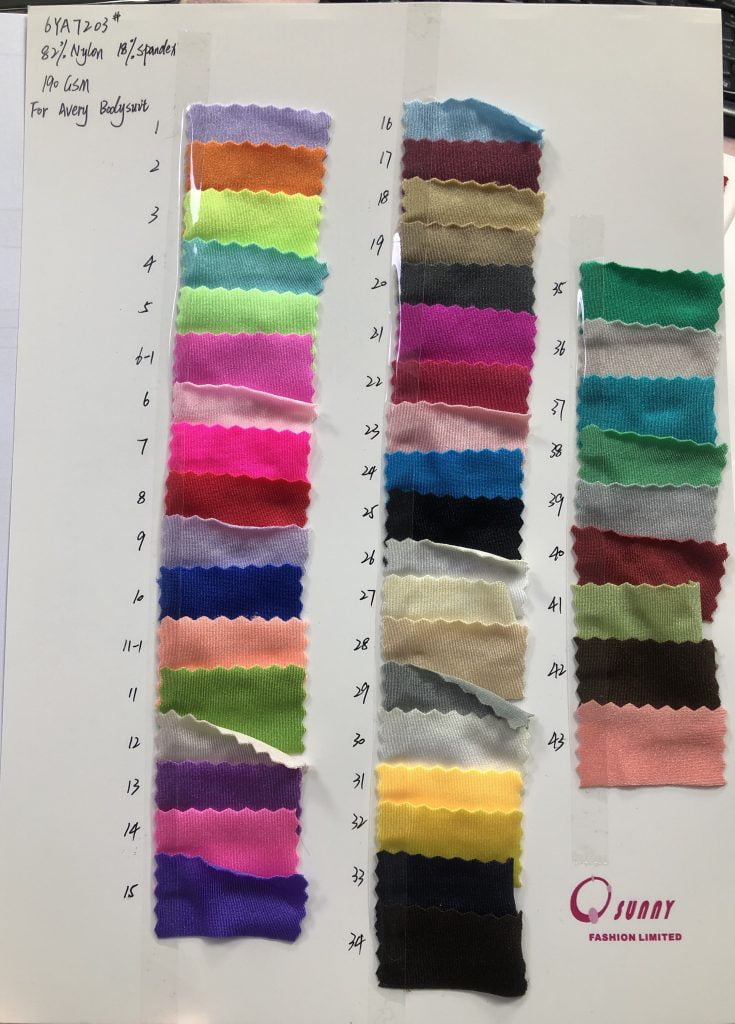
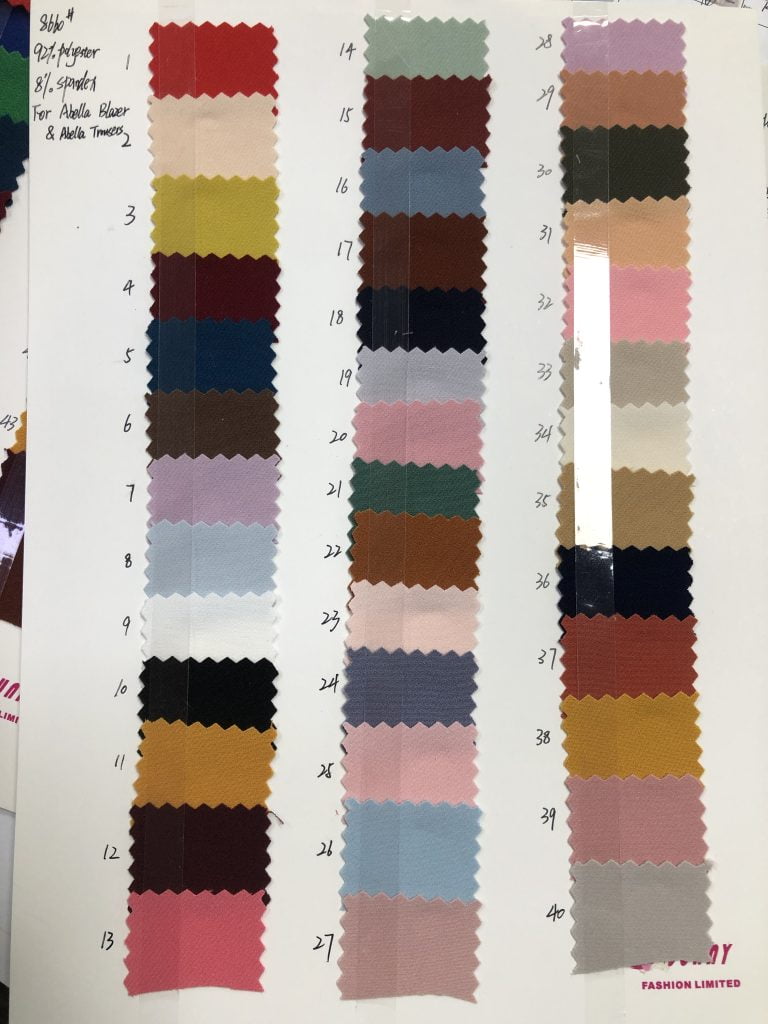
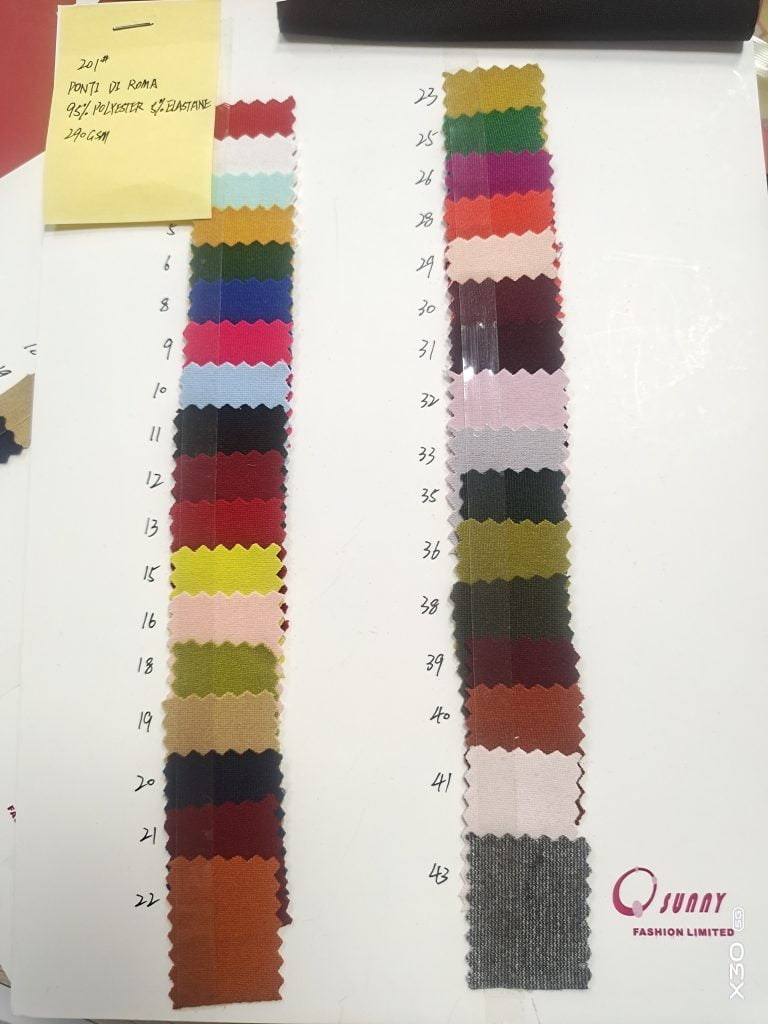
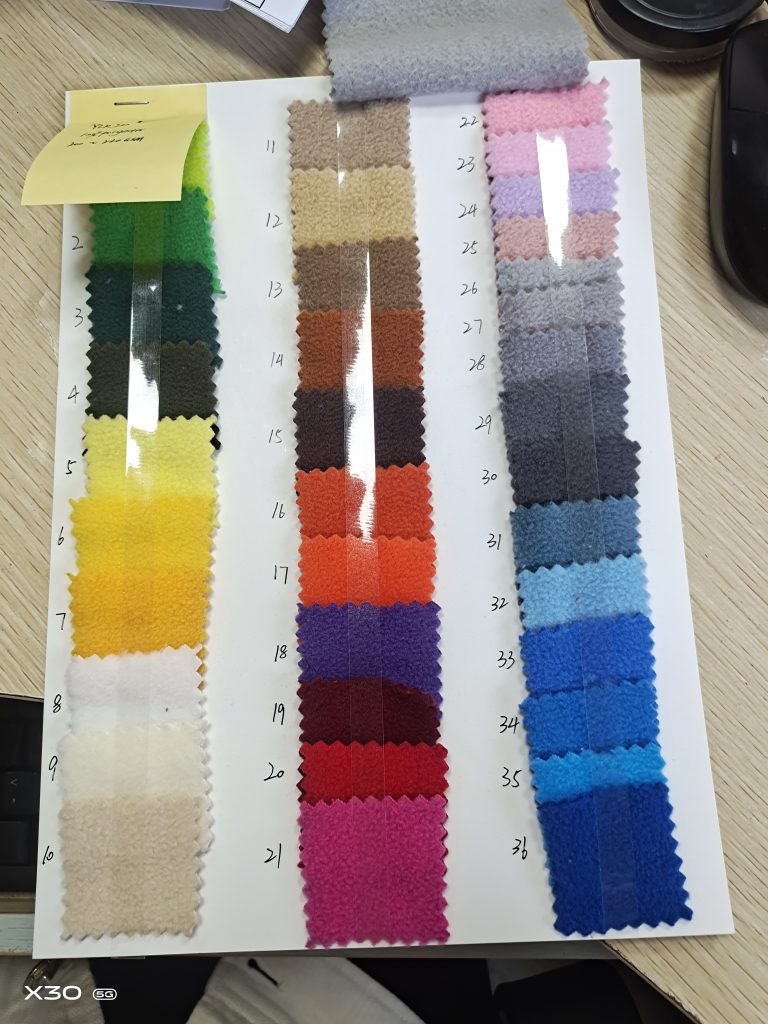
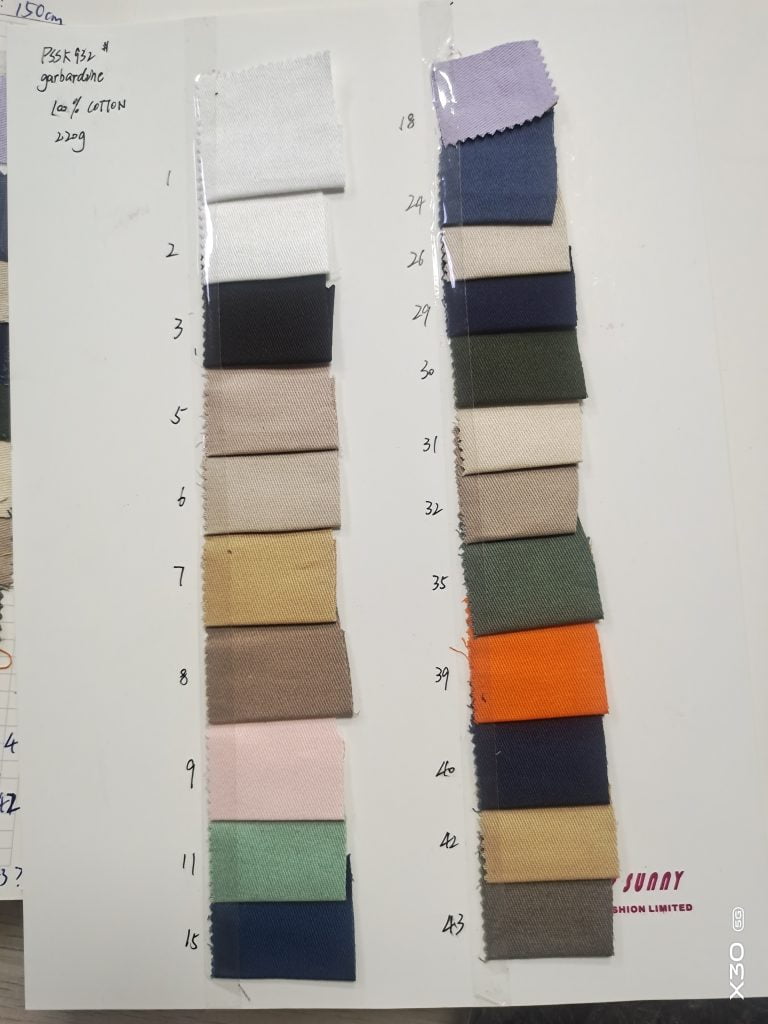
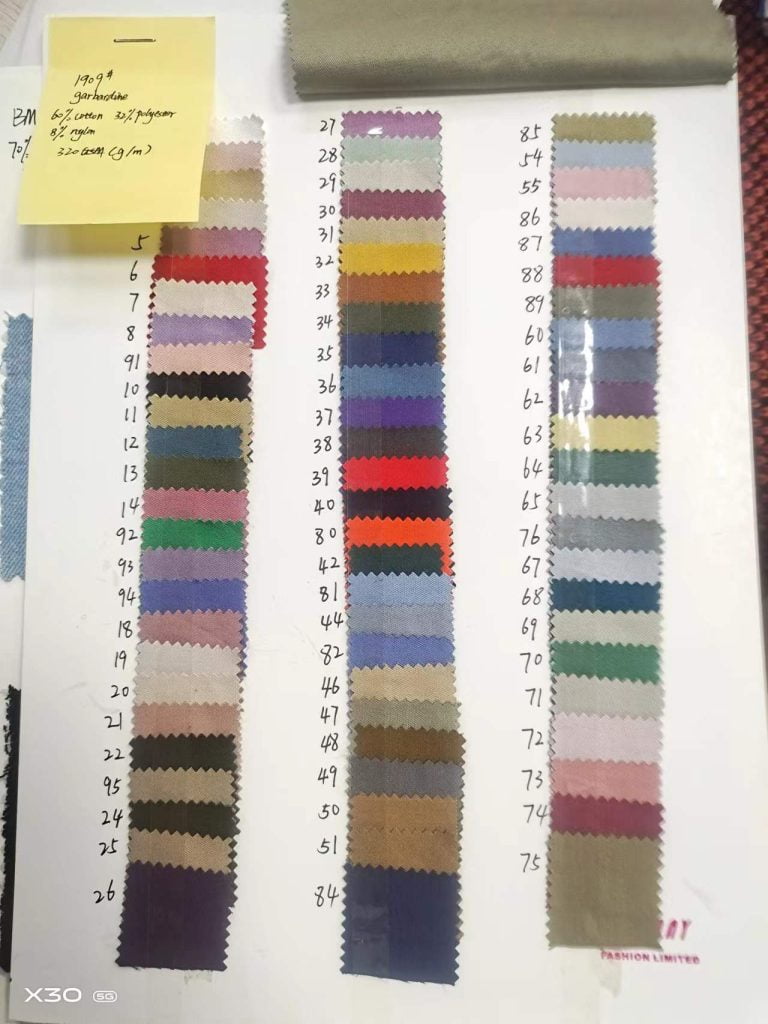
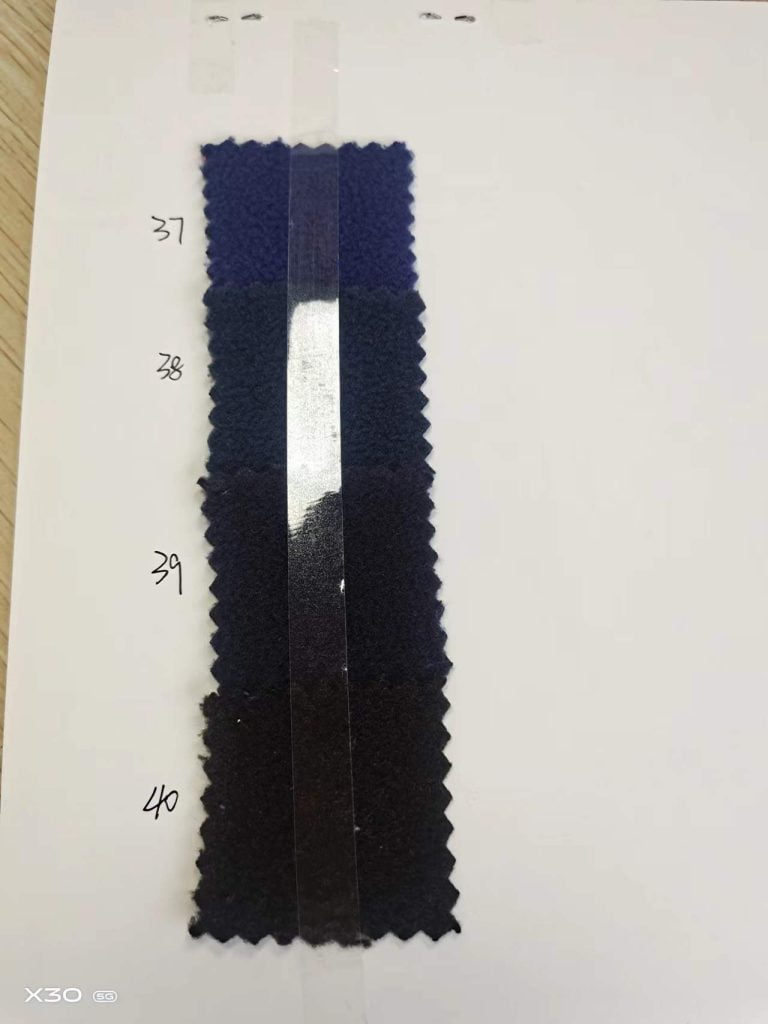
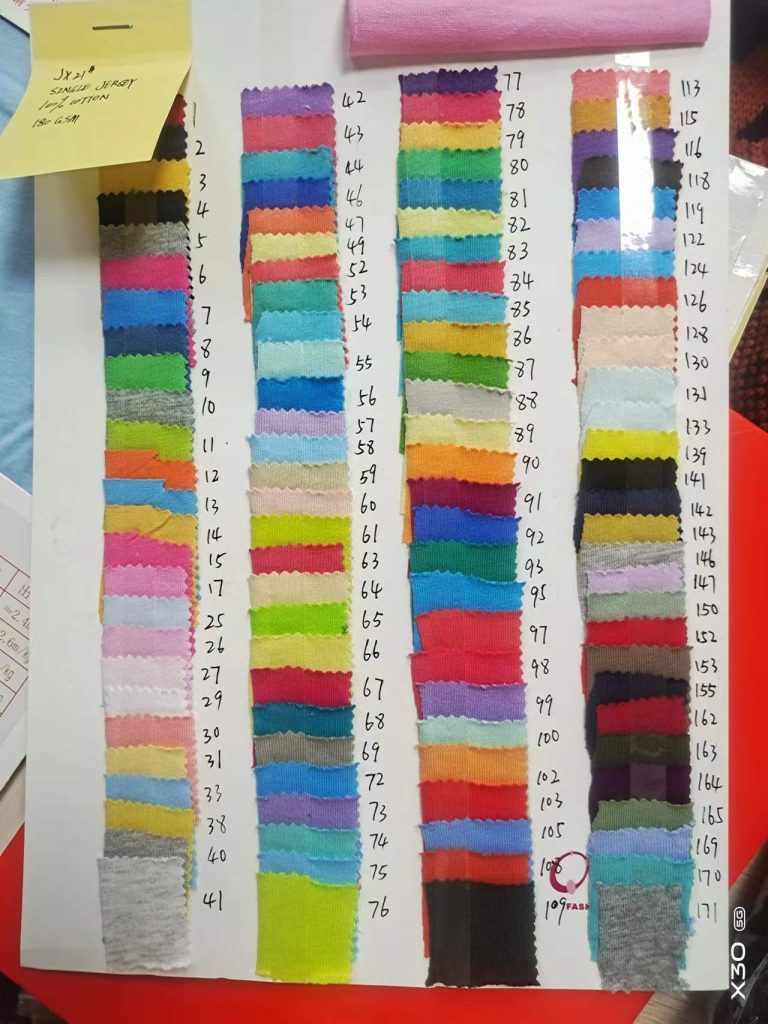
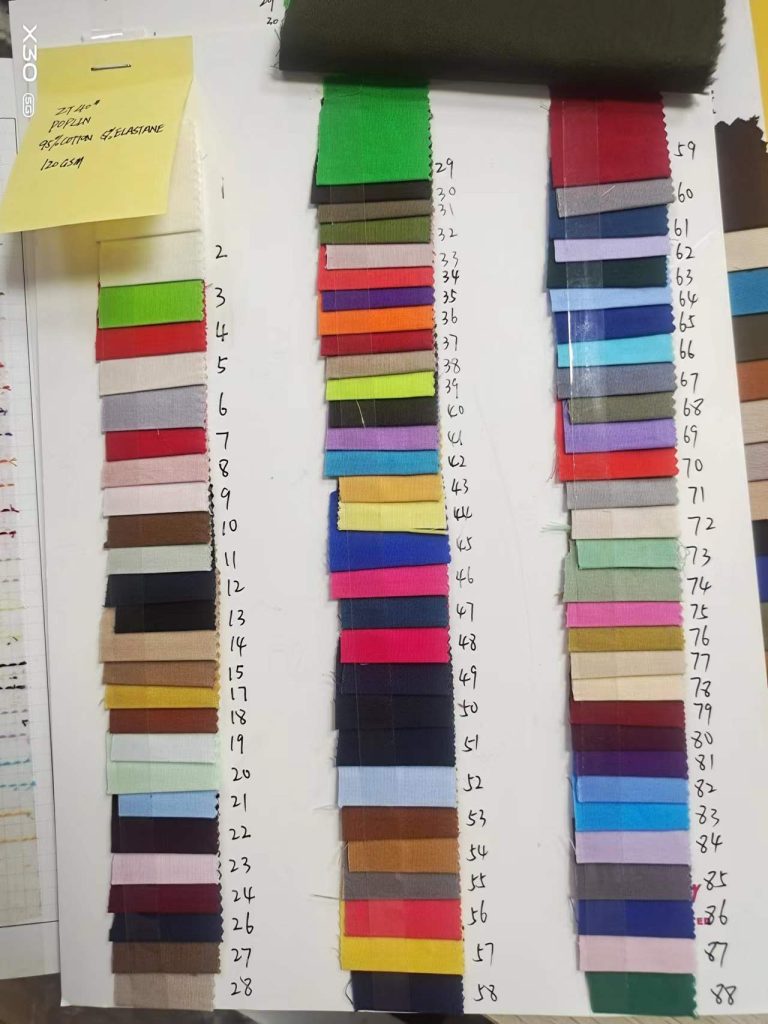
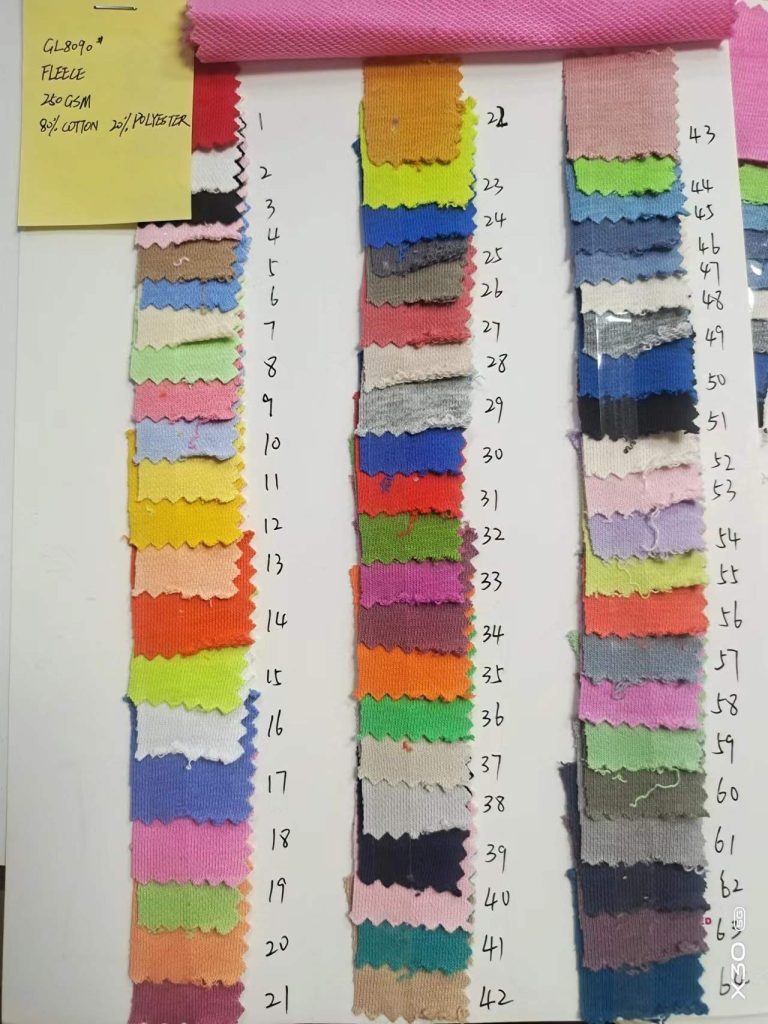
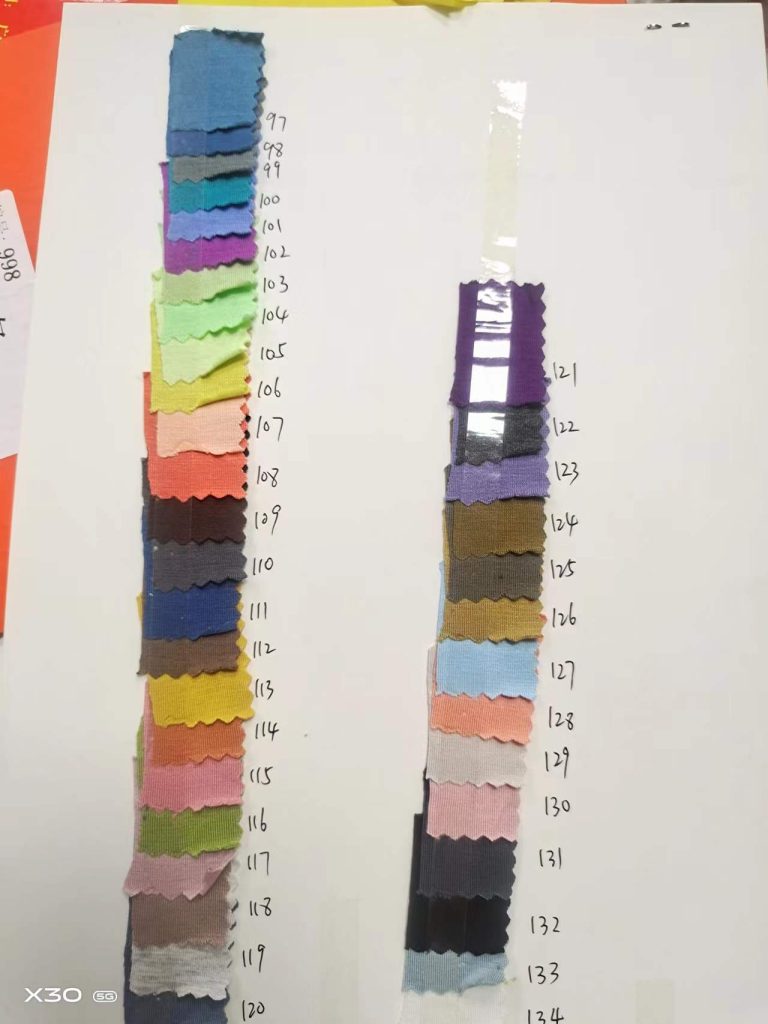